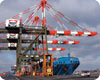
One of the world’s largest independent multi-user container terminal operators uses a network recorder platform and digital cameras to manage workflow as well as safety training.
Loading and unloading containers at one of the world’s busiest ports is a challenge, even when things go perfectly. In a major security video upgrade, one huge facility saw flexibility and cost saving in turning away from traditional cabling.
Demand for

Maher Terminals needed an enterprise video monitoring system with multiple camera views on dozens of management team member screens to support operations and workflow. The JVC system platforms on a network-based recorder.
COMPLEX WORKFLOW NEEDS
Unloading is even more difficult and requires skill and patience by the highly trained crane operators. In order to manage the workflow and support vessel loading/unloading operations, Maher Terminals operations management needed to upgrade the old digital video recording system to improve support for up to 16 container cranes. Maher is one of the world’s largest independent multi-user container terminal operators.
The cranes are only one area of operations management responsibility.
The other area of operations management responsibility is to monitor the entry/exit and grounds of the 455-acre facility, designed to process up to 13,000 semi-trucks per day. These trucks pass through to pick up or drop off containers in all kinds of weather and disabled/delayed trucks might wreak havoc in the carefully timed work flow at the facility.
Maher needed an enterprise video monitoring system that could provide multiple camera views on dozens of management team member screens to support operations and workflow. The video recording system had to be a powerful network-based recorder that could also serve up multiple camera views to dozens of workstations around the facility in real-time. The frames per second had to be flipped in favor of viewing with fewer frames used for recording. Typical security video surveillance installations require high frame count for recording rather than viewing, which is a different goal than managing operations.
NETWORK RECORDING PLATFORM
After an exhaustive search, JVC technology was selected as the network video recording platform because of the open architecture approach for enterprise scalability and capability to meet the Maher management team requirements for viewing in real-time.
The next step for the Maher team was to select cameras for the network video recording system. Maher’s existing IT network includes a powerful backbone of single mode gigabit fiber optic cabling with a high bandwidth wireless mesh network for hard to reach areas on the property. If an analog camera was the only solution, Maher would have encountered a huge cost just to provide coax cable to a critical entrance location. JVC’s cameras made the project economical because they plug into the wireless mesh network with no additional hardware and provide complete coverage of the entrance/exit over the wireless mesh link with full Pan/Tilt/Zoom control.
With the focus on crane operations and work flow around the yard, Maher’s management team currently has up to 20 simultaneous viewers operating 24/7. With JVC’s system, its operations staff now has the ability to see critical aspects of operations on the sprawling facility, enabling them to make more informed and faster decisions which help employees keep the work flowing. In the past, reliance on two-way radios for communications provided very limited insight into the nature and complexity of operations issues.
ALSO SAFETY APPLICATIONS
In addition to the operations staff reaping benefits from the new system’s network video live views, Maher Terminals’ safety department also uses live and recorded video streams for training purposes. The video provides an excellent platform to train operators on the safety aspect of the job and helping new employees understand the requirements of the yard and vessel operations.
As a result of the positive impact the network video recording system has had on operations, Maher Terminals is considering expanding the existing system in Port Elizabeth , New Jersey and new facility in Prince Rupert , British Columbia with similar network video recorder and camera technology.
SIDEBAR: The Advantage of a Fiber Backbone
When surveying a potential installation, some chief security officers may shy away from using fiber optics. When asked why, many state that fiber is too tricky to work with and that their technicians have neither the training nor the correct tools and testers to authoritatively handle fiber connections.
Smart installation companies also are concerned with what happens after the job is completed. How will they troubleshoot and fix balky equipment that is connected to fiber links? Although these concerns are valid, end-users and their systems integrators who don’t do fiber optics are missing a rich vein of opportunity.
Fiber is superior to copper cabling in every performance parameter.
EMI and RFI interference is vanquished because the signals traveling through a fiber are optical, generated by either a blinking LED or laser. Fiber can be installed in the worst electrical interference environments possible with absolutely no detrimental effects.
Fiber also provides great potential cabling distances. Inexpensive fiber devices can easily traverse up to two miles from end to end on multimode fiber.
The real gold mines are unused fiber links that are already in place.
The cabling industry estimates that more than 80 million “dark” fibers are installed in North America . These unused fibers are the result of the very low cost of individual fiber strands and the prevailing philosophy in the cabling industry, which is to always include extra fiber strands when installing structured cabling and backbone cables between telecommunications closets and separate buildings. Most often, fiber is owned by the IT department and it is a good way for security to partner with IT.